5 Common Motor Rebuild Mistakes & How to Avoid Costly Errors
Avoid motor rebuild mistakes by thoroughly inspecting components, cleaning parts, using proper torque specs, and choosing high-quality parts. Follow break-in procedures to ensure long-term engine performance and reliability, especially for heavy-duty trucks in demanding conditions.
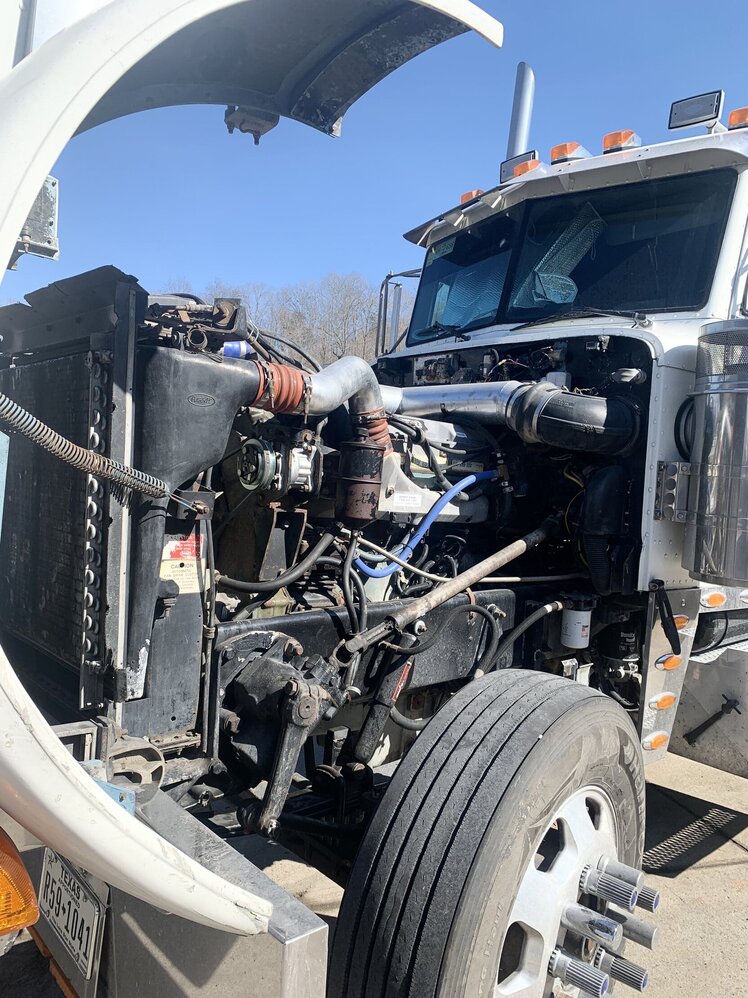
Rebuilding a motor is no small task. Whether refreshing an old engine or addressing significant wear and tear, a rebuild demands precision, expertise, and attention to detail. Unfortunately, even seasoned mechanics can make errors that lead to reduced engine performance or outright failure. For truck operators, avoiding these common motor rebuild mistakes can save time, money, and frustration. Let’s break down the top mistakes and how to sidestep them for a successful rebuild.
1. Neglecting to Thoroughly Inspect Components
One of the most common errors in a motor rebuild is failing to perform a detailed inspection of all components. Overlooking even a minor crack or wear on a part can lead to catastrophic failure. For instance, reusing worn pistons or connecting rods without proper measurements can compromise the entire rebuild.
To avoid this, always inspect components using precision tools like micrometers and bore gauges. Pay particular attention to cylinder walls, crankshafts, and valves, as these areas endure the most stress. In Oklahoma’s varying climate, frequent temperature shifts can exacerbate wear on engine parts, making thorough checks even more critical.
2. Skipping Proper Cleaning Procedures
Engines operate in a harsh environment, and rebuilding without thoroughly cleaning all parts is asking for trouble. Even tiny particles of dirt or metal shavings can cause significant damage, leading to reduced performance or engine failure.
Before assembly, use professional-grade cleaning solutions to remove debris, carbon buildup, and old oil residues from every component. Pay extra attention to oil passages, as blockages here can lead to inadequate lubrication—a death sentence for any engine. In Edmond’s dusty conditions, particularly during construction-heavy seasons, contaminants can easily infiltrate engines, making cleanliness even more crucial.
Quick Tips for Proper Cleaning
- Use a parts washer for deep cleaning.
- Blow out oil and coolant passages with compressed air.
- Ensure no lint or residue from cleaning materials remains on the components.
3. Using Incorrect or Subpar Parts
Rebuilding a motor requires precise parts that match the engine’s specifications. Using incorrect components, such as the wrong piston rings or oversized bearings, can result in poor engine performance or internal damage. Similarly, opting for cheap aftermarket parts to save money may compromise quality and longevity.
Always verify the compatibility of parts with the engine model. For heavy-duty trucks operating in Edmond, which often handle long distances and heavy loads, investing in high-quality OEM or trusted aftermarket components is essential to avoid premature failure. When opting for a motor rebuild, you want to increase performance so spending extra for quality components will enhance the longevity and efficiency of your engine.
4. Improper Torque Specifications
Incorrectly torquing bolts is a frequent mistake during motor rebuilds. Over-tightening can lead to stripped threads or warped components, while under-tightening can cause parts to loosen during operation. Critical areas like the cylinder head and crankshaft bearing caps require precise torque to function optimally. Refer to the manufacturer’s specifications for proper torque values and follow a consistent sequence, especially for components like the head gasket. Using a calibrated torque wrench is non-negotiable to ensure accuracy.
5. Skipping or Rushing Break-In Procedures
After completing a rebuild, many truck operators are eager to hit the road, but rushing the break-in process can lead to disaster. Newly installed parts, such as piston rings and bearings, need time to seat properly. Skipping this step can cause oil consumption issues, power loss, or even permanent damage to the motor. For truck operators in Edmond, where extreme weather can already strain engines, following break-in procedures is critical to ensure the rebuild holds up under local driving conditions.
During the break-in period:
- Use high-quality break-in oil to ensure proper lubrication.
- Avoid prolonged idling or heavy loads in the first 500 miles.
- Gradually increase RPM and load to allow components to settle.
Prevent Motor Rebuild Mistakes Today
Rebuilding a motor is a meticulous process that requires careful attention to detail. Dyess Truck and Trailer Repair offer services from thorough inspections to following proper torque specs and break-in procedures, to avoid these common mistakes. Our team’s motor rebuild will keep it operating for years. For Edmond, OK, truck operators, where reliability and performance are non-negotiable, these best practices can mean the difference between success and costly failure. With expertise in heavy-duty repairs and a commitment to quality, we’ll ensure your rebuild goes off without a hitch. Read our article to learn more on how to maximize your engine life.